In our last Terminal Tips blog, we reviewed API Bottom Loading Couplers and some of the common maintenance issues that we see. The next step is taking a closer look at the loading arms that are typically deployed at petroleum terminals around the globe. The loading arm design is a critical piece of the puzzle when building a successful, efficient terminal installation.
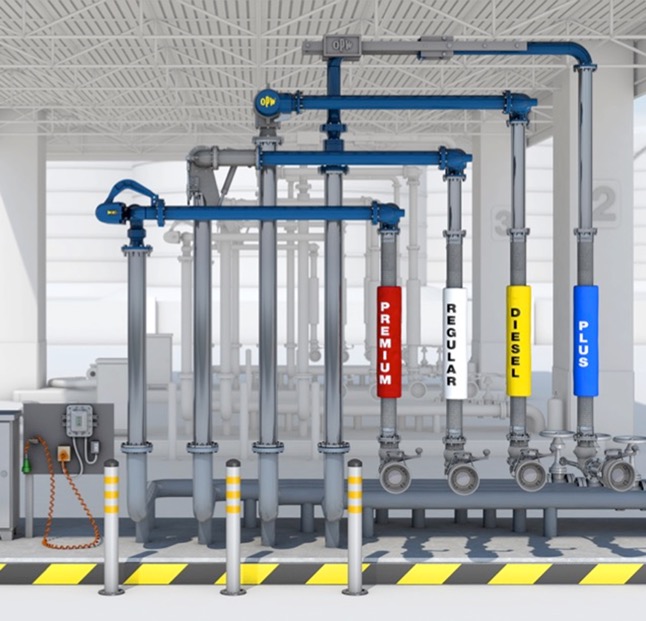
Types and Styles of Terminal Loading Arms
Many different styles of loading arms are deployed around the world. In many cases, a terminal operator may want or need to load as many as seven or eight products in a single lane/bay. In these circumstances, proper design is critical in ensuring a successful installation that allows for storage, deployment and full crossover. From torsion springs to counterweights to gas struts, loading arms should be designed to work in concert with one another while providing full coverage across the API envelope.
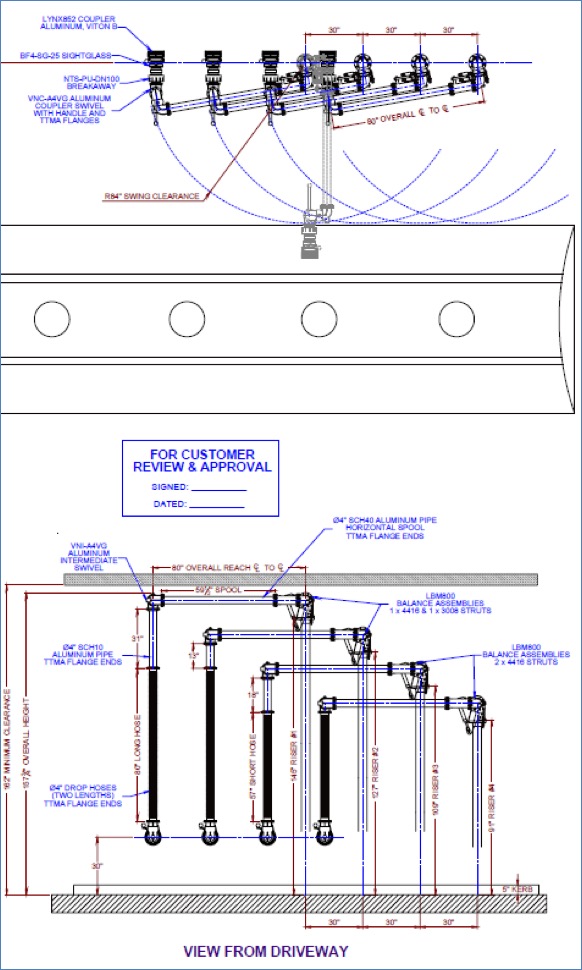
On a new installation, the main goal is to optimize the layout in order to make the operation as seamless as possible. On existing installations, you may have to work with a design that is less than ideal, but there are still steps you can take to optimize your situation.
- Counterbalancing. Are your loading arms properly adjusted? It is not uncommon to walk into a petroleum terminal and see loading arms that aren’t properly adjusted. A properly adjusted arm will put the API coupler in a rest position that is roughly the same height as the truck adaptor. In the United States, that height is roughly 30” off of grade. With the loading arm in this position, the operator doesn’t need to lift or pull to get the coupler connected to truck. In many instances, all it takes is a simple counterbalance adjustment to improve operation.
- Hose Lengths. Are your hoses the correct length? Again, the goal is to have the API coupler resting at roughly the same height as the truck connection. If the arms are properly adjusted and still not level with the truck connection, the hoses are likely not the correct length. Ensuring they are the correct length is another relatively simple adjustment that can greatly improve the operation.
- Travel Stops. Did you know that your loading arms likely have upward/downward travel stops? They can be set to limit the upward and downward travel of loading arms. If the terminal setup features lighting, overhead canopies, piping, etc. that the arms are constantly banging into, the use of travel stops is an easy way to resolve this situation.
- Coupler Spacer Spools. In some cases, the truck connection may be located deep under the belly of truck or within a cabinet. Simply installing a spacer spool, which are typically six to eight inches in length, between the coupler swivel and API coupler can help make those connections easier to access and complete.
- Isolation Valves. Adding an isolation valve near the API coupler can simplify maintenance, which is critical because the API coupler will likely need servicing more than any other component on the loading rack. When maintenance is required, do you want to drain the contents of the entire loading arm, which could be several gallons? Or, would you rather be able to close an isolation valve and have to collect only a small amount of product? So, the choice is a 55-gallon drum or a five-gallon bucket. In most cases, the five-gallon bucket would be the clear choice.
- Sight Glass. In addition to the isolation valve, adding a sight glass near the end of the loading arm is another option that may make a lot of sense. In this day and age where the use of additives is common, it is nice to be able to “see” what is flowing within the loading arm. Whether it is red dye for diesel or ethanol for gasoline, seeing is believing.
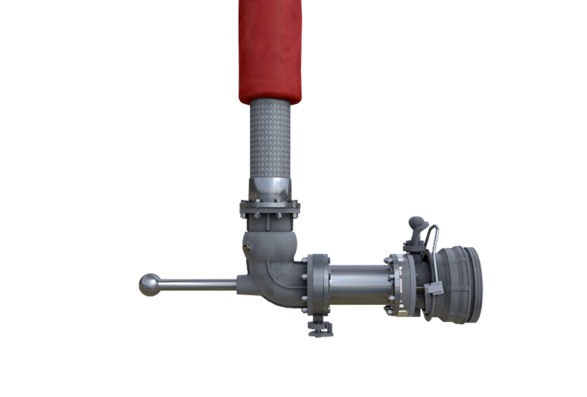
These are just a few things to consider when looking to improve the overall operational efficiency and effectiveness of terminal loading arms. For more information, please visit opw-es.com. In addition, we are always available to assist with any of your terminal loading-rack questions through our contact us page.