A real-world example of OPW Engineered Systems’ unique ability to confront a complex challenge and respond with the optimum solution played out recently at a high-volume bottom-loading petroleum terminal in Kentucky. Originally built in the 1940s, the terminal’s truck-loading lanes had undergone a number of “on the fly” upgrades, expansions and reconfigurations over the years that had ultimately resulted in an unorganized and inefficient loading operation. Specifically, the system had grown to consist of a hodge-podge of components that was cumbersome to operate due to poorly spaced and incompatible arms that not only led to loading inefficiencies, but also put strain on the drivers due to the non-ergonomic system design.
While the loading lanes and equipment may have worked as envisioned when they were initially constructed nearly 80 years ago, the progression of the layout to where it stood in 2019 was unable to deliver the expedited, efficient loading times that are expected in today’s fast-paced world. And, yes, over the years it’s safe to say the drivers had come to “hate” the arms and the way they operated.
In the search for a solution, the terminal operator reached out to a Cincinnati-based distributor for OPW Engineered Systems, Specialty Products and Systems. After bringing OPW in to survey the site, it was easy to see that the biggest issue was the fact the loading arms did not effectively cross over one another. This meant that it had become difficult for the driver to access the required arm without needing to move other arms out of the way first, or to load more than one compartment at a time.
Turning to its many years of experience, the OPW Engineered Systems engineering team created a new layout design that incorporated the ideal spacing and staggering of the arm mounts. For the equipment, OPW recommended short-range bottom-loading arms that are outfitted with LYNX API couplers.
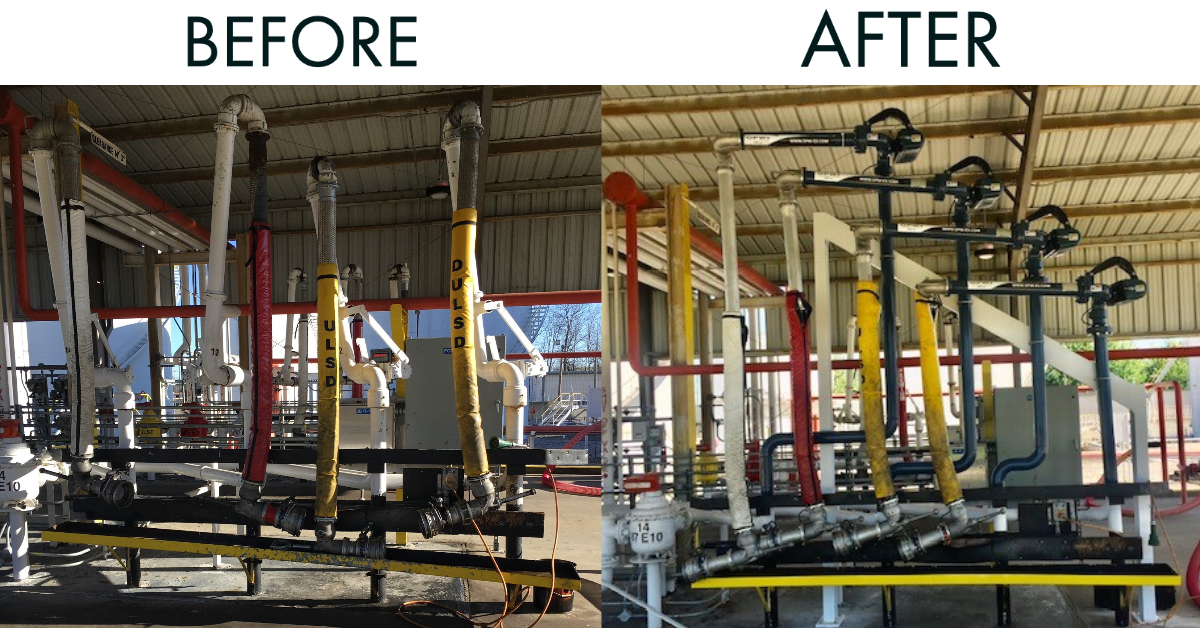
OPW’s SRH Bottom Loading Arms are short-range hose loaders that allow simultaneous connecting to and filling of up to three product lines. They are generally stored horizontally with only slight upward or downward movement required to align the coupler with the truck adaptor. LYNX Bottom Loading Couplers set the standard in dry-break API coupler performance through their ultra-durable stainless-steel collar and ability to ensure the loading-arm connection is not compromised even at surge pressures up to 500 psi (35 bar).
Additionally, OPW spec’d and designed new mounting piping for the truck lanes that enabled the loading arms to be installed in the optimal mounting configuration.
Today, the redesigned loading system features arms that are able to cross over and clear one another, which allows easy access to the desired arm and the ability to quickly and efficiently load multiple compartments at the same time. The arms are also more ergonomic in that they store and balance at roughly the same height as the truck adaptors. This means that little effort or strain is required from the drivers in order to connect and disconnect the arms to the truck adaptors and return the arms to their storage position when the loading process is completed. Finally, with all of the new system’s components sourced from the same supplier, it is easier to order, stock and track spare and replacement parts.
In the end, the customer was delivered the best possible outcome – in just six weeks from purchase order to product shipment – through a cooperative effort between local distributor Specialty Products and Systems, OPW’s engineering and design team, and OPW’s well-earned ability to provide a complete loading solution that meets the specific needs of the terminal’s operation.
This project truly showcased that “The OPW Difference” is much more than a catchy slogan; it’s the foundational DNA that enables OPW Engineered Systems to strive every day to consistently meet or exceed the expectations of its customers who demand the best solutions for the most difficult and unique fluid-handling challenges.