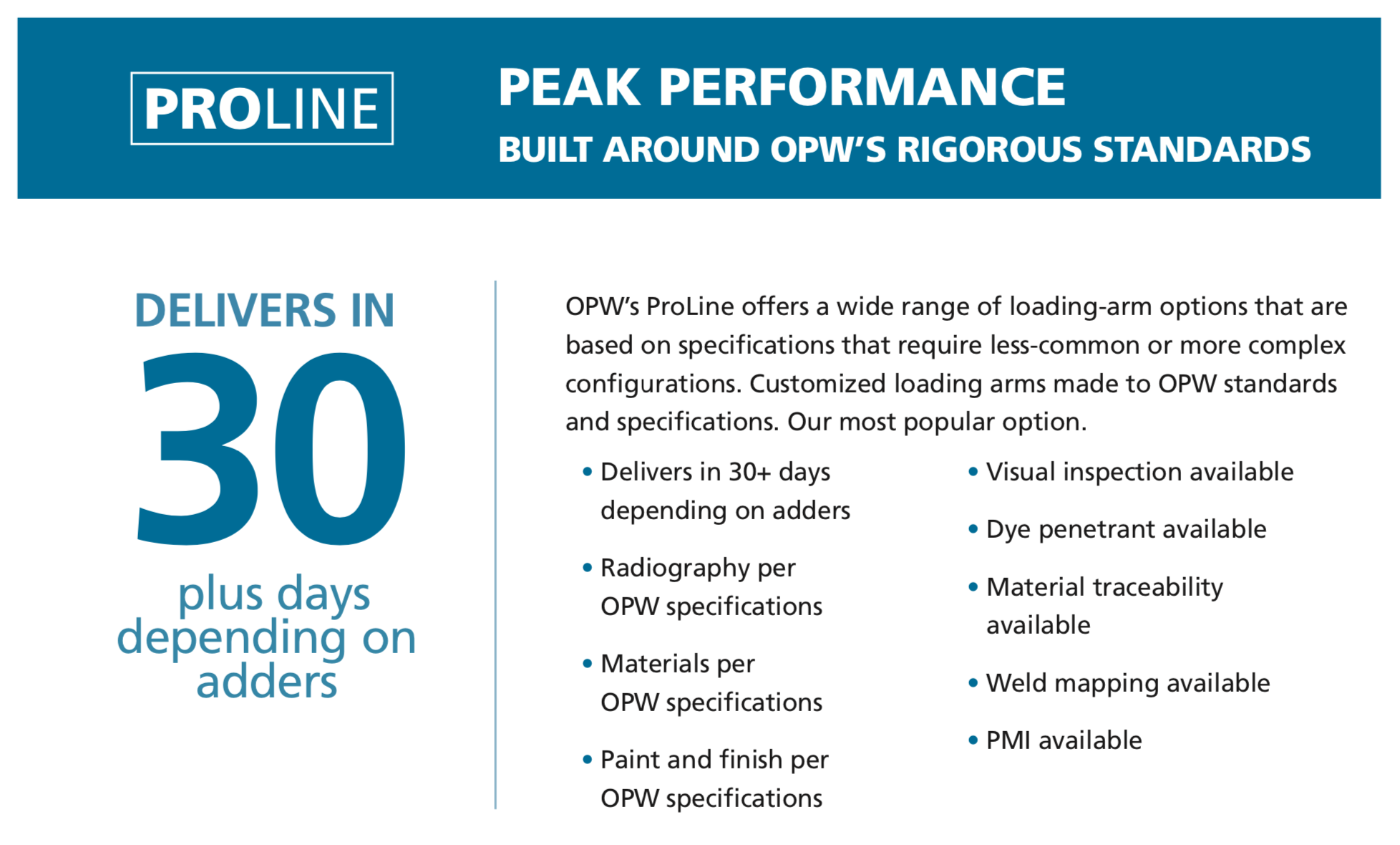
OPW’s 125-year-plus commitment to providing one of the safest, most reliable and most efficient storage-terminal loading-arm technologies has rightfully positioned it as one of the acknowledged leaders in the field. The latest manifestation of its expertise in this realm came in 2019 when the company announced that it had performed a top-to-bottom reimagining of its loading-arm business, with the creation of three distinct OPW Engineered Systems loading-arm families: StandardLine, ProLine and CustomLine.
While StandardLine consists of the most popular pre-engineered solutions that OPW offers, CustomLine provides the end-user a “you dream it, we make it” approach to creating a fully customized solution. ProLine combines the best of those two approaches.
Specifically, ProLine offers a wide range of loading-arm options that are based on OPW specifications that have been developed and refined through the analysis of many years of experience and end-user input. All ProLine loading arms use traditional setups as a foundation, but are fully configurable through OPW’s standard materials, procedures and testing methods. In other words, ProLine is a range of loading arms that is customized to the end-user’s specs, but blends in standard specifications, all while being able to be delivered in 30 working days or less.
To ensure that all ProLine loading arms meet the requirements for reliable, long-lasting, trouble-free performance, several non-destructive testing (NDT) operations can be performed as they are being built, including:
- Radiography: Anywhere from 5% to 100% of circumferential butt-welds per purchase order (PO) can be tested, with the radiography performed by a third-party ASNT inspector to the requirements of ASME B31.3 Normal Fluid Service regulations. Lots from which the 5% sampling are pulled will only include welds contained within a single PO.
- Visual: From 5% to 100% of purchase-order welds can be visually inspected by a third-party ASNT inspector to the requirements of ASME B31.3 Normal Fluid Service regulations. Lots from which the 5% sampling is pulled will include all weld work in the factory.
- Dye Penetrant: This can be performed on 10% to 100% of welds by a third-party ANST inspector per the requirements of ASME Boiler and Pressure Vessel Code V.
- Material Traceability: Traceable as-built map drawings of the wetted pressure-containing items will be provided for the system’s swivels, ASME pipes and ASME pipe fittings. Other add-on items must be reviewed for availability and can include disconnects, breakaways and hoses.
- Weld Mapping: As-built weld maps will be provided in the data package and will contain weld ID, weld date, weld procedure, and weld-wire lot number.
- Positive Material Identification (PMI): PMI is performed by a third-party X-ray fluorescence (XRF) analyzer that creates a chemical report with a traceable shot-location map. Only wetted, metal and pressure-containing items will bested, with PMI not available for carbon-steel or aluminum components.
The commitment of OPW Engineered Systems to creating systems and components that promote safe loading of hazardous and high-value materials at storage terminals leads to a never-ending search to both improve its current offerings and develop new ones that increase the standard of operations. The ProLine loading-arm family, as a member of OPW’s new three-pronged approach to developing components for loading-arm users, is a perfect manifestation of the company’s Defining What’s Next approach to addressing and meeting the unique needs of its channel partners.