What began three years ago as a quest to ensure the highest levels of safety at the rapidly growing and expanding OPW Retail Fueling facility in Smithfield, NC, culminated in a letter of recognition from the North Carolina Department of Labor (NCDOL). OPW Retail Fueling had been approved for participation in NCDOL’s prestigious Rising Star Program. The recognition was formally announced at the Annual NCDOL Carolina Star Program banquet, held September 17, 2015.
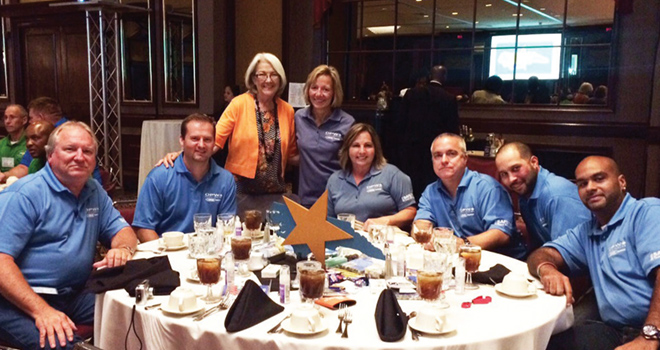
2015 Rising Star Team (left to right): Steve Brinchek, Greg Kennedy, Cherie Berry (NC Commissioner of Labor), Linda Townsley, Sherry Carter, Lou Duffy, Luis Mirabal, and Kelvyn Mateo.
A letter written by LaMonte D. Smith, NCDOL Recognition Program Manager, and co-signed by Cherie K. Berry, NCDOL Commissioner of Labor, stated, “It is quite obvious that your site makes safety and health practices a vital part of your company’s operation.”
“This particular statement was perhaps the most gratifying part of receiving this prestigious recognition,” stated Mike McCann, VP & General Manager of OPW’s Retail Fueling business unit. “When we started this journey three years ago, we were beginning to experience substantial, rapid growth. We owe it to the employees and each other to provide a safe and healthy workplace. Knowing that we’d be bringing on board a lot of new people, we wanted to ensure that our safety processes were scalable and the best they could possibly be.”
“We view our people as our number one priority,” McCann continued. “So at OPW, we have always placed great
emphasis on safety. We made a lot of investments on physical improvements to the facility, but we knew we needed to do more to have everyone really embrace a true safety culture. We decided that pursuing “Star” status would be a way to really focus the team, and be a great way to get everyone in the organization involved. As a result of this process, we feel like we have now exponentially elevated our safety practices and created a high level of safety culture throughout the facility. I could not be more proud of the entire workforce.” The Carolina Star Program is North Carolina’s Voluntary Protection Program (VPP), designed to recognize and promote effective safety and health management systems. OPW is one of only 155 out of 253,000 North Carolina companies to achieve the state’s prestigious Star certification.
The Carolina Star Program
As outlined on the NCDOL website, the Carolina Star Program is designed to recognize and promote effective safety and health management systems. In Star, management, labor and OSHA establish a cooperative relationship at a workplace that has implemented a strong program.

Program Process:
- Management agrees to operate an effective program that meets an established set of safety criteria.
- Employees agree to participate in the program and work with management to ensure a safe and healthful workplace.
- North Carolina OSHA initially verifies that the program meets Star criteria. North Carolina OSHA then publicly recognizes the site’s exemplary program and removes the site from routine scheduled inspections lists (OSHA may still investigate major accidents or fatalities, valid formal employee complaints and chemical spills).
- Becoming a Star participant shows employees and the community that OPW is committed to be a leader in occupational safety and health.
Carolina Star — Recognizes worksites that are self-sufficient
in their ability to control hazards at the worksite.
Rising Star — Recognizes worksites that have good safety
and health programs, but must take additional steps to reach
Carolina Star quality
The NCDOL is passionate and equally serious about elevating safety in the workplace. They impose stiff requirements, but they also firmly believe that all companies that are committed and disciplined are capable of achieving the Star standard. They also believe the benefits of being a Star site are worth striving for and maintaining, which include:
- Improved employee motivation to work safely, leading to better quality and productivity.
- Reduced workers’ compensation costs.
- Recognition in the community as a leader.
- Improvement to safety programs through internal and external review.
- A safer workplace as Star participant sites generally experience 60 to 80 percent fewer lost workday injuries than would be expected of an “average” site of the same size in their industries.
The Three-Year Journey to Becoming a Rising Star
McCann’s team methodically embarked on this Star quest by first creating two new positions: Safety Manager and Safety Coordinator. A strong leadership team was then selected, many of whom were rising stars: Greg Kennedy, Director of Operations; Steve Brinchek, Facilities & Safety Manager; Linda Townsely, Director HR/Global Safety; Sherry Carter, Buyer II; Lou Duffy, CNC Lead; Luis Mirabal, Safety Coordinator; Kelvyn Mateo, 10 Cell Assembly Lead.
For the last two years, representatives from North Carolina OSHA accepted a total of four invitations to the Smithfield facility, two per year. During each of their visits, three-day audits were administered of the facility and its safety practices. And for three consecutive years, OPW personnel attended the Carolina Star Conference to gain insight and understanding into what was required to become a Carolina Star Program (VPP) facility.
“We were determined to achieve the highest level of safety possible,” stated Greg Kennedy, Director of Operations for OPW Retail Fueling. “We dedicated the time, people and money to make sure we satisfied all 18 elements of consideration in order to validate that we were VPP ready. We did it right. Our management and associates got fully engaged, which was essential to our success.”
“I think one of the most important aspects of the program was the mentoring program,” commented Steve Brinchek, Facilities & Safety Manager for OPW Retail Fueling. “We were teamed up with three different Carolina Star companies: John Deere, Mt. Olive Pickle and Balfour Beatty. We visited their facilities, and each shared with us their safety programs and best practices. This gave us tremendous insight into how great workplaces result from a safety-first culture. This was invaluable learning that we could put into practice
at our site.”
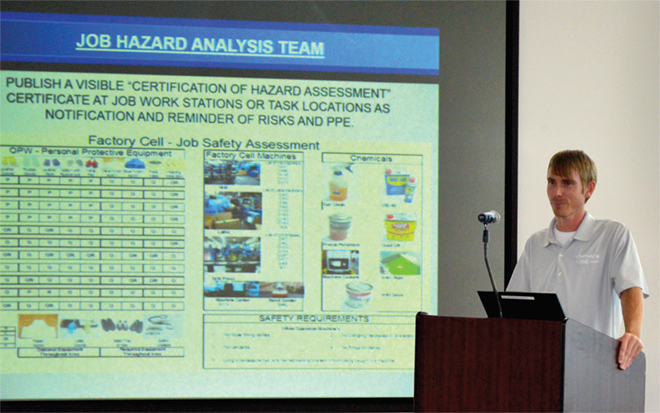
Josh Price, Manufacturing Engineer, presenting for the Job Hazards
Analysis Safety Team
Since OPW already considered safety as part of its DNA, it was well positioned to demonstrate the five main elements for Star consideration: Management Commitment, Employee Involvement, Hazard Identification and Evaluation, Hazard Prevention and Control, Safety and Health Training. In fact, the company already had more than 41 percent participation on active safety teams, and 82 percent associate participation in the company’s annual Health and Wellness Fair.
“OPW has worked diligently to create and sustain a robust safety and wellness culture,” stated Linda Townsley, OPW — Director HR/Global Safety. “We have very motivated and caring associates, so we were very confident that we’d get all the participation that we needed to further elevate our safety and health rating. People here truly care about each other and making this the safest workplace environment possible.”
A high level of participation is a cultural norm for OPW.
As testimony to this fact, the company currently has fourteen robust and active teams: Corporate VPP Team, FCS Steering Committee, Ergonomics, Safety Policy Review, Incident Investigation, Safety Incentive / Awards, Job Hazard Analysis, Mission Statement, Safety Concerns, Wellness, Safety Disciplinary, Safety Audit, Forklift Training, and First Aid, all of which served to illustrate to the NCDOL that OPW was worthy of Star participation consideration. All of these teams went through some level of Star training, depending on their role by a third-party safety trainer.
“All of our shop associates attend a 30-minute safety huddle per week,” explained Luis Mirabal, Safety Coordinator for OPW Retail Fueling. “And all administrative associates attend a 30-minute huddle monthly. As an added incentive, we also employ a popular Be–Safe Bingo card game. It is very popular throughout the entire company.”
With respect to the Bingo game, Luis pointed out that the cards are only given to associates who attend all of the safety huddles each month. Additional cards are given for Find-It/Fix-It ideas. There are three winners per quarter on the Find-It/Fix-It program, so the competition is often very vigorous, and the results are always astounding.
The company also conducts an annual safety slogan contest and creates an annual safety calendar to encourage associates to to implement safety best practices at home with their families.
As further testimony to how widespread the commitment at OPW Retail Fueling is, one only needs to look at the
number of safety-oriented Kaizens completed in 2014... an astounding 300!
“We feel like we now have an ingrained safety culture at OPW,” said McCann. “It is quite evident to anyone who visits our facility. Great people have created a great working environment here in Smithfield. Of course, in the spirit of continuous improvement, we know we will never be completely satisfied. There is always more to do. All the credit goes to our safety teams and to every associate who works here every day. They’re the ones who make this a great... and safe... place to work.”
Adding credence to McCann’s statement, OSHA agreed. As part of the Star participation criteria, a three-person OSHA team conducted a vigorous three-day evaluation and audit of policies and procedures of the OPW Smithfield facility. To validate first-hand the OPW safety culture, the OSHA audit team interviewed almost every associate in their workcells, on every shift. OSHA’s findings qualified OPW Retail Fueling as compliant.
Areas of Excellence Identified
As part of the evaluation process, OPW was required to submit a written program that included the critical elements and sub-elements of a basic Occupational Safety and Health program, which was reviewed by the Carolina Star Evaluation Team. These elements included, but were not limited to:
- Management commitment and leadership
- Planning and evaluation
- Administration and supervision
- Safety and health training
- Hazard identification and evaluation
- Hazard prevention and control
- Employee involvement and participation
- Contractor safety
Other safety and health program elements reviewed included an exhaustive list of: general occupational safety and health policies and work processes; disciplinary policy; safety and health committees; OSHA injury and illness recordkeeping forms; safety audits; incident investigations (near miss / first aid); personal protective equipment assessments; industrial hygiene protection (hazard communication, hazardous chemical clean up, and hearing conservation); blood borne pathogens training; confined space entry; emergency action plan; fall protection; fire protection; hand/power tool protection; hot work permits; ladder safety; lockout / tag out; material handling; powered industrial truck operations; and pre-job training.
OPW Retail Fueling continues to strive for improvement. One of their most important goals is to create the optimum safe and healthy workplace. For instance, they will conduct continuing education for hazard recognition programs to ensure that employees will recognize hazards created by themselves or other employees, and develop the knowledge to correct them when possible.
As part of the NCDOL Star Review, areas of excellence were identified and shared with OPW. Management and corporate commitment were identified as the top two areas of excellence, followed by:
- Overall safety record of OPW Smithfield
- Over a three-year period, its plastic pipe and pipe fitting NAICS class of trade, the company’s average Total Recordable Case (TRC) for 2012, 2013 and 2014 was 3.4 or 35 percent below the 21-3 Federal Bureau of Labor Statistics rate of 5.2
- The employer’s Days Away, restricted or Transferred (DART) rate for 2012, 2013, and 2014 was 2.2 or 33 percent below the Federal BLS rate of 3.3
Based on the evaluation, the NCDOL Carolina Star Evaluation Team confirmed that OPW Retail Fueling met all of the requirements to qualify for the Carolina Star Program and was approved for participation as a Rising Star workplace.
“I am particularly proud of our team in Smithfield,” stated OPW President David Crouse. “When you read the list of identified areas of excellence compiled by the NCDOL you can’t help but be impressed. It makes me incredibly proud, because it validates the exceptional job everyone in Smithfield has been doing. Safety and Continuous Improvement come second nature to Mike McCann and the entire Smithfield team.”
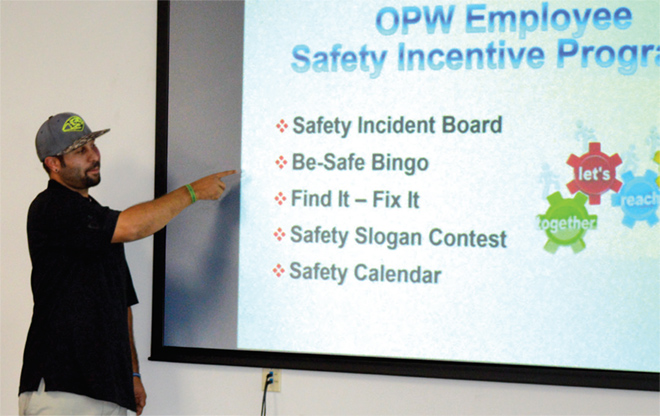
Safety Coordinator Luis Mirabal presents the Safety Incentive Program
From Dover to OPW to Smithfield, creating the safest and healthiest work environment possible is clearly an important initiative for all. Every member of the OPW Retail Fueling organization should be proud. They are all rising stars!